
NASA Rotor 67 is redesigned through blade profiling. The adjoint method requires about twice the computational effort of the flow solution to obtain the complete gradient information at each operating condition, regardless of the number of design parameters. This paper presents the application of a viscous adjoint method to the multipoint design optimization of a rotor blade through blade profiling. With the constraint that the relative change in the flow rate is less than 0.5% and the total pressure ratio does not decrease, within the acceptable time in engineering, the adiabatic efficiency of Rotor 37 at design point increases by 1.02%, while its surge margin 0.84%, and the adiabatic efficiency of Stage 35 0.54%, while its surge margin 1.11% after optimization, to verify the effectiveness and potential in engineering of this new tool for optimization of axial compressor blade.

A new engineering optimization tool is constructed by combining the surface parametric control method, the IABC algorithm, with a verified Computational Fluid Dynamics (CFD) simulation method, and it has been successfully applied in the aerodynamic optimization for a single-row transonic rotor (Rotor 37) and a single-stage transonic axial flow compressor (Stage 35). The Improved Artificial Bee Colony (IABC) algorithm, which significantly increases the convergence speed and global optimization ability, is adopted to find the optimal result. Bezier surface is adopted as parameterization method to control the suction surface of the blades, which brings the following advantages: (A) significantly reducing design variables (B) easy to ensure the mechanical strength of rotating blades (C) better physical understanding (D) easy to achieve smooth surface. The pressure reduction due to sweep and dihedral is more limited than what could be expected from wing aerodynamics.Īn aerodynamic optimization method for axial flow compressor blades available for engineering is developed in this paper. With forward dihedral and axial skew the backflow region is reduced in size and axial extent, but a more significant hub corner stall region is found. Forward sweep and circumferential skew shorten the radial migration path, but more flow separation is present near the hub. The backward shape variety generally gives negative aerodynamic effects. Current results show that forward sweep and circumferential skew are beneficial for higher total-to-total efficiency and that higher total-to-static efficiency can be obtained by forward dihedral and axial skew. Based on a validated Computational Fluid Dynamics simulation method, effects of sweep, dihedral and skew in axial and circumferential directions (in forward and backward direction) on the aerodynamic performance of small hub-to-tip ratio fans are investigated, with a linear stacking line. For such fans, extensive regions of backflow are present behind the fan near the hub.
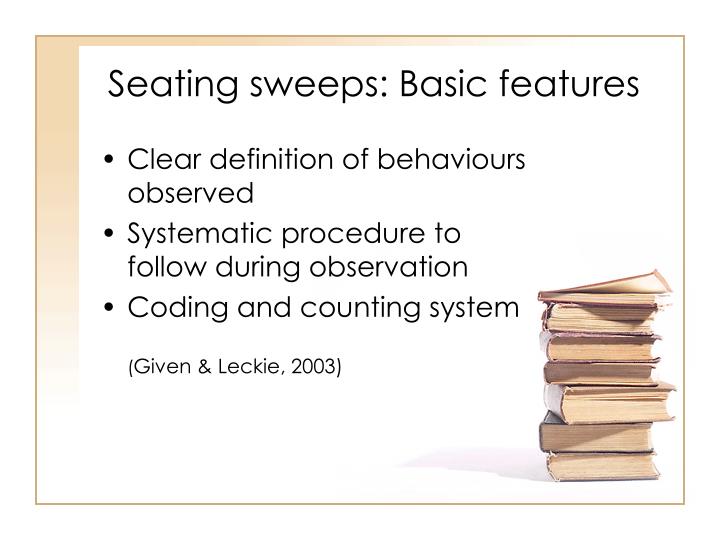
However, only few studies for fans with small hub-to-tip diameter ratio have been reported. Investigations on axial fans with medium to high hub-to-tip diameter ratio have shown that forward sweep of blades can give improved aerodynamic performance, especially the total-to-total efficiency. Optimization of their aerodynamic performance is important, for which using sweep, dihedral and skew of the blades' stacking line form an important method. Axial fans with low hub-to-tip diameter ratio are used in many branches of industry.
